- Training
Lean Six Sigma Training
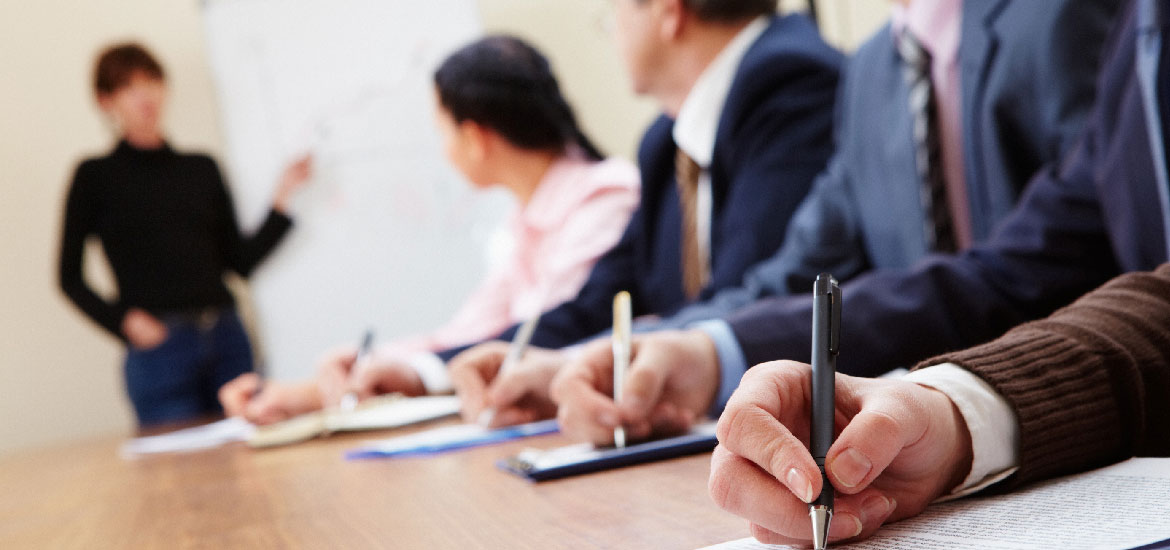
SUMMARY:
In this module, you will learn to understanding of Six Sigma basic and why it is more important to control your processes that make final control your product after it is produced. Also, you will get introduced to different disciplines of Lean and Six Sigma, and tool be used in process optimization, defects reduction and root cause analyzing. The course will give you a far more effective utilization of your resources you spend your money on!
There are three ways you can get a better earning, A) sell more, B) reduce cost or C) be more efficient. Effectiveness will bring you far more.
VIBENHOLT - MBA, LSS Black Belt instructor, PRINCE2 trainer certified
CONTEXT:
Six Sigma is a management philosophy. How to apply it in a company is different to the scope of products or services provided to the customer. But it is a simple facts that if you do not deliver what the customer want or deliver product with defect you will lose on market, it is also known that the more your processing your product during manufacturing the more expensive it is, and the more monetary cost you lose if the production is wrong. Six sigma philosophy aim to remove the possibility for errors or defects as early in the value stream as possible – addressing the right specification to the supplier, designing the product to meet the customers expectation and is producible in a way where errors can be avoided, finally optimizing the production process the most efficient way. Without making defects.
This series of training course give you the tools to meet the customer requirements with a high quality and by that a lower production cost
At the completion of this first Course, participants will be able to:
• Optimize your effectivities of the work processes
• Understand the concept of the Lean Six Sigma philosophy
• Understand which tools to be used in the Six Sigma methodology
• Constructive participate in improvement or problem-solving projects
• Prevent waste of resources
Competencies that are addressed:
Primary Competency Categories:
Customer Experience — Creates an environment with customers to maintain a positive long-term relationship. Get the customer in focus and let him feel we deliver a reliable product, produced in a reliable process. Thus we deliver on time.
Customer requirements — Identify what the customer needs are in specific requirements to the production. Make sure you and your costumer is aligned on definition on defects – so you can control it.
Related Competency Categories:
Initiative — Proactively makes things happen. Control improvement project to success, secure corrective actions are really solving the problem.
Results Oriented - Passionate about winning. With a more efficient production process you will be the market leader.